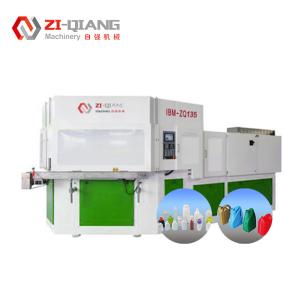
A. 金型設計と設備の高い適応性 • 複合金型構造:射出ブロー成形機の金型は通常、射出金型、ブロー金型、および離型機構で構成され、これら3つを正確に連携させることができます。金型位置決めは、高精度ガイドピンとガイドスリーブを採用し、サーボモーターで駆動される開閉金型システムと連携します。位置決め誤差は0.02mm以内に制御でき、射出およびブロー成形段階での金型の位置が完全に一致するようにし、位置ずれによる製品欠陥(ボトル本体のずれや壁厚の不均一など)を回避します。 • 耐高温金型材料:高温殺菌を必要とする製品(医療用ボトルなど)の場合、金型は耐熱合金材料(H13熱間金型鋼など)で作られ、独立した冷却水回路が装備されています。120℃を超える成形環境でも安定性を維持でき、熱膨張と収縮による金型の精度への影響を回避します。
B. 特殊形状製品の優れた成形能力 • 複雑なボトル形状のワンステップ成形:ハンドル、溝、特殊形状の肩部など、複雑な構造を持つ中空製品(化粧品ポンプヘッドボトルや医療用サンプリングボトルなど)の場合、射出ブロー成形機は、射出成形段階での予備成形設計を使用して、ブロー成形中に金型の細部を正確に充填し、その後の組み立てや二次加工を必要とせず、生産工程とコストを削減します。 • 薄肉化と重量比の正確な制御:"薄肉大容量"製品(壁厚がわずか0.3mmの500mlボトルなど)を製造できます。射出成形圧力とブロー成形ストレッチ比を最適化することにより、ボトルの強度を確保しながら原材料消費量を削減でき、飲料、日用品、および軽量化に対する高い要件を持つその他の分野に特に適しています。
C. 生産プロセスの高いトレーサビリティ • データ記録と分析機能:ハイエンドの射出ブロー成形機には、産業用IoT(Internet of Things)モジュールが装備されており、各バッチの製品の生産パラメータ(射出温度、ブロー成形圧力、成形時間など)、機器の動作状態(モーター負荷、金型温度など)、および品質検査データ(ボトルの重量、壁厚など)をリアルタイムで記録して、追跡可能な生産ファイルを形成できます。 • MESシステムとの連携:工場の製造実行システム(MES)との連携をサポートし、生産計画、原材料バッチ、完成品の倉庫保管など、プロセス全体のデジタル管理を実現し、企業が品質トレーサビリティ、プロセス最適化、およびコンプライアンス監査(製薬業界のGMPトレーサビリティ要件への適合など)を実施するのに役立ちます。
D. 低メンテナンスと長寿命設計 • 主要コンポーネントの高い耐久性:スクリューとバレルは、耐摩耗性合金(38CrMoAlA窒化処理など)で作られており、耐腐食性と耐摩耗性があり、10万時間以上の耐用年数があります。油圧システムは、高精度フィルター(ろ過精度3μm)を使用して、油汚染による故障を減らし、メンテナンス頻度を減らします。 • 予防メンテナンスのリマインダー:機器制御システムは、動作時間とコンポーネントの損失データ(金型の開閉回数、モーターの稼働時間など)に基づいて、メンテナンスのリマインダー(潤滑油の交換やフィルターの清掃など)を自動的に発行し、生産に影響を与える突然のダウンタイムを回避します。
E. 省エネとインテリジェントアップグレードのトレンド • サーボ省エネ技術の普及:新世代の射出ブロー成形機は、ほとんどがフルサーボドライブを採用しています(射出、金型の開閉、ブロー成形はすべてサーボモーターで制御されます)。従来の油圧ドライブと比較して、エネルギー消費量は30%〜50%削減され、動作ノイズは75デシベルと低く、環境保護と労働安全衛生基準を満たしています。 • AI支援プロセス最適化:一部のハイエンドモデルは、人工知能アルゴリズムを導入しており、過去の生産データを学習することにより、最適なプロセスパラメータ(原材料バッチの違いに応じて溶融温度を調整するなど)を自動的に推奨し、新製品のデバッグサイクルを短縮し(従来の2〜3日から数時間に短縮)、上級技術者への依存を減らします。